La saldatura è un’unione che avviene tra metalli uguali o diversi, comunque compatibili tra loro.
Per unire due pezzi di metallo, il metodo più semplice, sicuro ed economico è quello di saldarli, beninteso quando è possibile eseguire la saldatura.
La saldatura è un fenomeno fisico, che consiste nel liquefare parte dei pezzi da unire tra loro e nel lasciarli diffondere l’uno nell’altro. Quando i metalli si raffreddano sono diventati un unico pezzo. Le saldature possono essere eseguite in due maniere diverse: con o senza materiale di apporto.
Saldatura con apporto
Nel primo caso di saldatura si adopera, di solito, una bacchetta di metallo (elettrodo o barretta di ferro o altre leghe da saldatura) che viene fusa con facilità e fatta colare sopra le due parti da saldare come se fosse una colla.
Naturalmente bisogna riscaldare anche le due parti, in modo che il materiale d’apporto si aggrappi ad entrambe.
La saldatura è detta autogena se il metallo base partecipa alla costituzione del giunto, fondendo insieme al metallo d’apporto, che è di composizione assai simile.
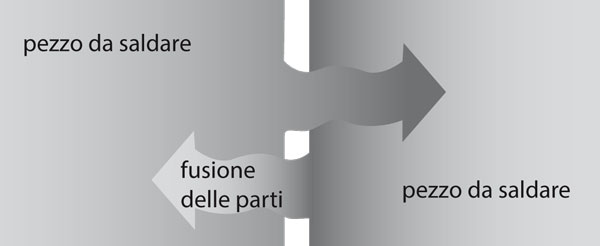
Saldatura autogena. La saldatura è l’unione di due metalli mediante la fusione delle parti scaldate fino a raggiungere il color rosso, così che il metallo si comporti come una colla e i due pezzi si fondano insieme.
Si chiama autogena perché ottenuta senza materiale d’apporto.
La saldatura è detta, invece, eterogena, o anche brasatura, se il metallo base non è portato a fusione, mentre il giunto è generato dal solo materiale d’apporto, che aderisce come un liquido viscoso e solidifica.
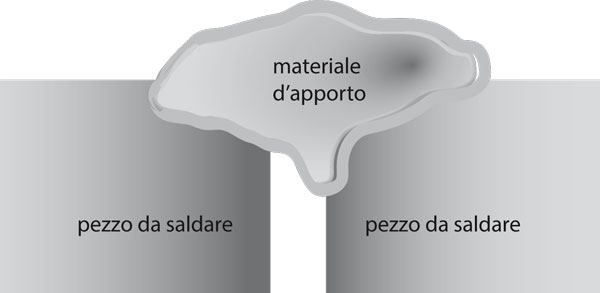
Saldatura eterogena o brasatura. La saldatura può essere eterogena perché eseguita con materiale di apporto: si adopera una bacchetta di metallo che viene fusa con facilità e fatta colare tra le due parti da saldare, dopo averle ben scaldate affinché il materiale di apporto si aggrappi. In questo caso si chiama più correttamente brasatura e può essere di tipo forte o dolce.
Saldare con apporto di materiale consiste nell’accostare le due parti che debbono essere saldate e nel riempire la fessura con metallo fuso. Questo metallo, da solo, non è sufficiente, di solito, per riscaldare in maniera opportuna i lembi delle parti da saldare e per questo motivo mentre si fonde il metallo d’apporto si riscaldano anche le parti, ma senza raggiungere la temperatura di fusione, non necessaria, anche se particolarmente utile per migliorare la mescolanza dei metalli che debbono essere congiunti.
Saldatura ad arco e saldatura alla fiamma
Le tecniche di saldatura con apporto di materiale sono sostanzialmente due: quella alla fiamma, ottenuta con diversi tipi di combustibile e comburente, entrambi allo stato finale gassoso, o quella ad arco voltaico, ove non occorre né combustibile né comburente, e che può avvenire in qualsiasi condizione, anche nel vuoto oppure sott’acqua, purché si disponga dell’energia elettrica necessaria.
Il materiale d’apporto si presenta quasi sempre sotto forma di bacchette, perché questo è il suo aspetto fisico più pratico, che si lavori sia alla fiamma sia con l’arco voltaico.
Le bacchette possono essere dello stesso metallo delle parti da saldare, come ad esempio il ferro o l’ottone, oppure di leghe che semplifichino la saldatura di metalli “difficili”.
Sempre per facilitare la saldatura, impedendo ad esempio l’ossidazione, le bacchette possono essere rivestite di particolari composti non metallici che galleggiano sul bagno fuso proteggendolo.
Con alcuni accorgimenti si riesce a saldare molto bene anche l’alluminio, purché si operi con particolari attrezzature ed in presenza di gas inerti, come l’azoto, che evitano la “bruciatura” del metallo (che ha forte tendenza all’ossidazione), ossia la perdita dei componenti, in quanto si tratta quasi sempre di leghe.
Saldatura senza apporto
La saldatura senza apporto, invece, consiste nel riscaldare le due parti (solitamente di ferro, perché con altri metalli la saldatura senza apporto di materiale o funziona male o non funziona affatto) fino a raggiungere il color rosso ed oltre, fin verso i 1300 °C.
A questa temperatura il ferro incomincia a scintillare, gli atomi perdono il loro potere di coesione e possono scorrere con facilità gli uni rispetto agli altri e compenetrarsi.
Il ferro si comporta a questo punto come se fosse una specie di mastice.
I pezzi da saldare vengono sovrapposti parzialmente e quindi vengono compressi con un maglio, una pressa, a martellate, e le molecole si mescolano, si compenetrano come un pettine fra i capelli. Quando il metallo così unito si raffredda, diventa un pezzo unico. Sembra facile. però ci sono piccoli inconvenienti.
Ad esempio quello della presenza dell’ossigeno, che può combinarsi con il ferro, formare una crosta, la tristemente famosa scoria di ossido.
Per eliminare questo inconveniente occorre unire un disossidante come il borace (una polverina che fonde e rende fluida la scoria) che assorbe l’ossigeno eliminandolo dalla saldatura. Questo tipo di saldatura è in uso anche oggi, perché facile da ottenere con una piccola fucina a carbone, che raggiunga senza difficoltà i 1600 °C, specie se si usa il sistema a ventilazione forzata.
Brasatura a stagno e a gas
Anche se nel linguaggio normale viene comunemente chiamata saldatura, quella a stagno è una brasatura, perché la fusione non riguarda i pezzi da unire, ma solo il materiale d’apporto: quest’ultimo, formato da una lega di piombo e stagno, permette di realizzare giunzioni solide con una temperatura relativamente ridotta.
Nel settore della lattoneria (canali di gronda, scossaline ecc) questa tecnica un tempo assai diffusa è stata sostituita da giunzioni con mastici al silicone; conserva invece un’importanza fondamentale nei campi dell’elettrotecnica e dell’elettronica, cioè là dove non è richiesta una particolare resistenza meccanica e si tratta di lavorare su pezzi di dimensioni assai ridotte: le basse temperature in gioco ed il brevissimo tempo richiesto dal lavoro, infatti, non creano problemi nemmeno ai componenti più delicati.
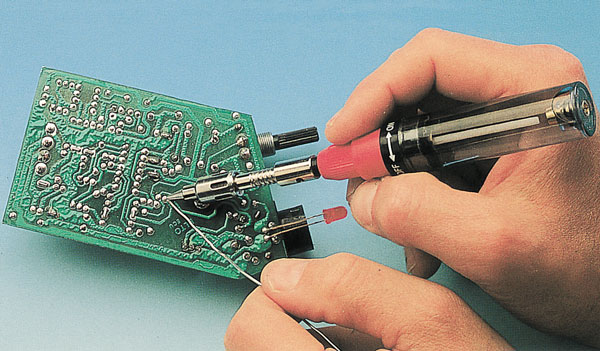
STAGNO E GAS. Di uso ormai generalizzato tra i professionisti il saldatore a stilo a gas, che non produce una fiamma visibile, è alimentato dal serbatoio contenuto nell’impugnatura (si ricarica come un accendino), funziona in modo molto simile alle stufe a gas catalitiche (quelle senza tubo di scarico dei fumi).
Attrezzatura per saldare
Per saldare senza troppe difficoltà è bene che gli elementi da unire siano tagliati a perfetta misura e con l’angolazione voluta: anche in questo caso il mercato offre una discreta gamma di soluzioni, dai supporti per smerigliatrice (con capacità di taglio limitata) alle troncatrici a disco abrasivo alle più recenti segatrici a nastro.
Detto in altre parole, chi intende lavorare il ferro deve prevedere anche l’acquisto di una macchina che permetta di sezionare le verghe e di preparare i diversi elementi di ciò che si intende costruire, con un occhio di riguardo alla possibilità di lavorare in serie (più pezzi di uguale misura) ed alla sezione massima dei profilati che si vogliono sezionare (verificare, di ogni macchina, la capacità di taglio a 90 ed a 45°).
È del tutto illusorio pensare di cavarsela col seghetto manuale o con la smerigliatrice.
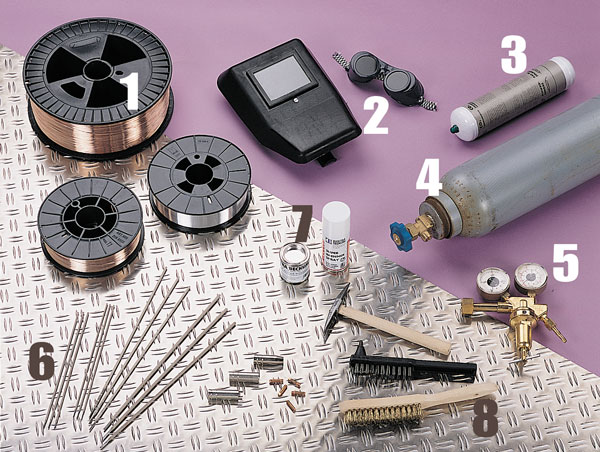
Tutti i tipi di saldatura richiedono sia l’impianto base (saldatrice, bombole) sia una serie di accessori e di materiali di consumo: il materiale d’apporto è un elettrodo (6) nella saldatura ad arco, una bacchetta di ferro di lega in quella a fiamma ed un sottilissimo filo (pieno o animato, di ferro o di inox), avvolto su bobine di diversa capacità (1), per saldare a filo continuo; in quest’ultimo caso si usano spesso bombole di gas inerte, a perdere (3) o ricaricabili (4) e sono essenziali i dispositivi di regolazione (5).
Servono inoltre maschera o occhiali per proteggersi la vista (2), prodotti chimici per disossidare (7), martelli e spazzole (8) per pulire il cordone di saldatura dalle scorie.
La lavorazione del ferro richiede anche un minimo di attrezzatura di base che accompagni la saldatrice: a parte l’indispensabile kit di saldatura (pinze, cavi, maschera, spazzola e martellina), serve anche una smerigliatrice angolare (meglio con disco da 115 mm, più leggera e maneggevole) per tagliare i pezzo o per rifinire i cordoni.
Indispensabile un discreto corredo di strettoi per bloccare i pezzi da saldare; per le giunzioni d’angolo, poi, esistono morse specifiche, capaci di mantenere nella giusta posizione elementi tagliati a 45°.
Saldatura ad arco
La saldatura elettrica si chiama “ad arco” perché, quando l’elettrodo tocca la superficie, scocca l’arco voltaico generando il cratere nel quale si fondono il metallo dei pezzi e quello d’apporto.
Esistono diversi sistemi di saldatura che sfruttano l’effetto dell’arco voltaico, ma quello più diffuso prevede l’utilizzo di materiale d’apporto sotto forma di elettrodi: questi sono costituiti da una bacchetta di metallo (con diametro da 1,6 a 4 mm) rivestita con una sostanza disossidante. Questa tecnica è senz’altro preferibile a livello hobbistico, perché permette di realizzare rapidamente ed a costi molto bassi giunzioni solide ed affidabili, a patto però che i pezzi presentino uno spessore non inferiore al millimetro. Le saldatrici di tipo più diffuso (e più economiche) erogano corrente alternata e possono affrontare, in genere, solo il ferro; quelle ad inverter erogano invece corrente continua e saldano anche l’acciaio inox.
Saldatura a filo
Le saldatrici a filo sono di dimensioni contenute; la bombola di gas che serve per saldare acciaio inox e alluminio mantiene nella zona di fusione un ambiente protetto.
Nelle saldatrici a filo continuo l’elettrodo è costituito da un lunghissimo e sottile filo metallico, avvolto su una bobina e capace di uscire con continuità dalla pinza (che qui si chiama torcia); il filo può essere pieno (in questo caso per saldare serve anche una bombola di gas inerte che protegga il metallo fuso dall’ossidazione) o animato: il filo è cavo ed è ripieno di disossidante (si può saldare il ferro anche senza l’apporto di gas). La saldatura a filo continuo è efficace anche su pezzi sottili ed è assai più facile da imparare e da eseguire rispetto a quella ad arco: molto dipende dalla bontà della macchina o, meglio, dalla possibilità di regolare con precisione sia la corrente erogata sia la velocità di uscita del filo.
Dove saldare
La soluzione ideale è quella di lavorare all’aria aperta o in locali fortemente arieggiati, ossia con porte e finestre sempre spalancate per eliminare rapidamente i fumi di saldatura, i gas della combustione e rinnovare l’ossigeno.
Un altro punto importantissimo è relativo al banco di lavoro.
Non si può pretendere di saldare ad arco o alla fiamma sul banco di legno del falegname o su quello dell’aggiustatore meccanico.
è indispensabile possedere un tavolo metallico, anche di dimensioni modeste, 600×600 mm, ricoperto da una pesante lamiera per la saldatura ad arco e la saldatura a stagno o gas liquido, sulla quale sia possibile occasionalmente poggiare mattoni refrattari.
Un banco per saldare può anche essere montato su rotelle, e tirato fuori, magari all’aperto, solo al momento dell’impiego, oppure può essere ospitato nel laboratorio quando le sue dimensioni e l’aerazione consentono di lavorare in ambiente chiuso o semichiuso.
Se il laboratorio è ubicato in una cantina dalla scarsa ventilazione non basta aprire porta e finestra: occorre anche una buona ventilazione forzata.
Non bisogna dimenticare, poi, che imparare a saldare è un ottimo presupposto per costruire un gran numero di manufatti, dal portavasi in metallo fino alla ringhiera della scala o alla cancellata di recinzione: in questi casi il pur utile banco di saldatura diventa del tutto inadatto, perché le dimensioni dei pezzi in lavorazione sono di gran lunga superiori alle sue possibilità.
È quindi opportuno, magari anche per acquisire un po’ di esperienza, affrontare prima di tutto la costruzione di cavalletti metallici, capaci di sostenere i diversi elementi durante l’assemblaggio.
Devono essere registrabili in altezza, in modo da poter disporre i pezzi in piano anche se si sta operando in un cortile: a questo proposito conviene sfruttare i normali scatolati metallici in commercio che, per fortuna, hanno misure che permettono interessanti soluzioni.
Uno scatolato quadro da 30×30 mm, ad esempio, è spesso 2 mm e quindi presenta una cavità di 26×26 mm, all’interno della quale può scorrere senza fatica uno spezzone da 25×25 mm: basta quindi forare il pezzo esterno, saldare un dado in corrispondenza del foro ed inserire un bullone di fermo per bloccare gli elementi nella posizione voluta.
una guida meravigliosa! grazie